There’s an urban legend that back in the day foundry muller operators could taste green sand and determine if the sand needed more clay or water, and if it was properly mulled. Nowadays just about every foundry in North America has automated compactibility controllers attached to their green sand muller to provide this critical information. While it’s great that this function is now automated; have foundries lost touch with the vital signs of their green sand system now that they no longer have a “hand in the sand?”
The frequency and way foundries trend and report data vary greatly. While some foundries only look at the data on the screen at the machine, (which means they only see what is happening right now), other foundries export their data into a database to use to track trends. In this article, we will look at trending daily sand data, and how to use results to determine variability in the sand system.
Compactability Targets: +/- 3 and +/-1
Proper compactability is critical to making good molds. High compactability can cause excess water, which potentially could result in poor surface finish, gas defects, soft molds, or stickers. Low compactability can cause molds to break and sand inclusion defects.
My favorite metric to track is the percentage a foundry is within +/- 3 of their compactability target. When the target compactability is 40, how many times was the measured result between 37-43? The same goes for +/-1 of target. While targets should be foundry specific, I suggest 85% within +/-1, and 95% within +/-3. Evaluating the percentage of the time the sand was within +/-3 this month compared to last month can be a quick check. This is an easy metric to share daily, weekly, and monthly to communicate the sand performance with molding and maintenance teams.
If the metric is 10% lower today than yesterday, it should signal that something is off. Start evaluating what else was happening during that time, such as temperature fluctuations, clay to water ratio, or operation of the compactability controller. Most often, the temperature fluctuates during times of lack of control. The quickest and easiest check is ensuring you are using the full amount of your return sand storage. Another item that can affect the sand temperature is changes in the sand-to-metal ratio. However, this is much less controllable. The most dependable way to reduce variation in temperature and moisture is a sand cooler.
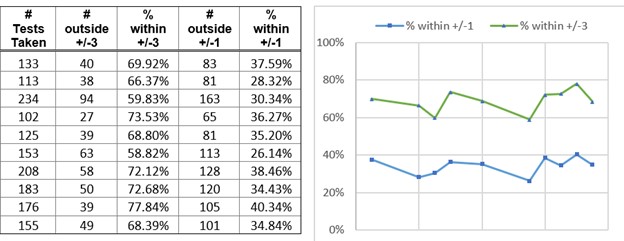
Example Report illustrating compactability performance.
Temperature Control Compactability (TCC) functions on compactability controllers optimize water additions based on temperature. Ideally the water added is the exact amount needed to activate the clay. When the sand is hot, some water will be used to cool the sand, and the remainder to activate the clay; therefore, more water is required when the sand is hot than if at ambient temperature.
To account for moisture loss as the sand travels from the muller discharge to the molding line, the TCC can be programmed to add additional water at elevated temperatures. The foundry can adjust the TCC offsets if it is deemed the moisture loss is having greater or lesser impact on compactability. If there is a lot of fluctuation at specific temperature ranges, it may help to evaluate these settings. There is a possibility that the offset is too great or too low for the temperature range.

TCC offsets can be adjusted to optimize sand properties.
Conductivity
Conductivity is used as a relative measure of moisture in the return sand coming into the muller; typically, a wetter sand mixture will result in a higher conductivity measurement. Multiple conductivity measurements are taken and averaged together to report a single value. Plotting time by conductivity can highlight concerns that should be addressed. If there are many consecutive readings in a row at 0.35 it likely means the sand is too hot and you need to find ways to cool the sand.
If there are large fluctuations in conductivity readings, or receiving 0.35 readings at non-elevated temperatures, check the conductivity probes to ensure they are in the sand, and are reading correctly. A best practice is to monitor the difference between conductivity probe readings. By checking the difference between probes, it can help identify a probe fault. Again, targets will vary by foundry, but many foundries strive for conductivities between 0.75-1.5, without large variation between data points.
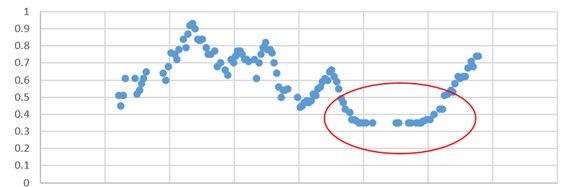
Example of multiple 0/35 conductivity readings in a row.
Water Addition
A good practice is to verify that water requested = water actual. Moisture in molding sand activates the clay bonds and is classified as either combined or free water. Controlling the moisture content of green sand should be maintained within a narrow range. Moisture in the green sand can affect muller efficiency, working bond, and available bond. It plays a part in nearly every green sand property, except grain fineness. Correlations can be seen between moisture content and compactability. Excess moisture can result in gas related defects, high strengths, lower permeability, and lower flowability. Low moisture produces dry friable sand and can be difficult to mold.
Batch Weight
The batch weight is the largest factor in determining water and clay additions. It is important that batch weight stays consistent from batch to batch. The simplest way to improve repeatability is to slow down the sand addition rate. A typical cycle allows over 45 seconds to weigh up the next batch, but many weigh the entire batch in under 5 seconds. Slowing down the speed could potentially reduce variation and improve accuracy. Also, a daily check of the batch hopper weight while empty is also important. The tare weight should be no more than 1% of the normal batch weight. If the weight is more than 1%, it is suggested to inspect the batch hopper for issues.
Green Strength
Green compression strength indicates the maximum compression stress the sand mixture is capable of sustaining. It is used to determine the amount of clay addition to a green sand system. Sand to metal ratio, clay content, compactibility, and additives can affect green compression strength. Low green compression strength indicates good flowability but can result in broken molds and poor pattern draw. Low green strength can be caused by low clay content, dry sand, an issue with the muller. High green compression strength can result in broken molds, poor flowability, and difficulties at shakeout.
When data is erratic or fluctuations are greater than normal, it is important to check the automatic compactability testing equipment to ensure the wipe-off is aligned and the sample cup is full. If secondary tests confirm the same trends, then start to look at what else has changed in the system. Trending sand data and reporting understandable metrics aids in troubleshooting and determining root causes throughout the foundry process. Repeatable sand properties ensure the sand is strong enough to hold up to the thermal stresses at the mold-metal interface. The sand system is telling us what to do, we just need to ensure we are monitoring and listening.